How Windset Farms is transforming greenhouse agriculture
Windset Farms® grew from humble origins. In 1996 Steven and John Newell began the business on their family farm in British Columbia (BC). Steven outlines how the company grew into the powerhouse it is today. “We began with a four-acre bell pepper greenhouse. By 2003, we obtained a marketing agency license from the BC Vegetable Marketing Commission, which allowed us to establish our own brand in BC – a pivotal moment in our growth. We’ve come a long way since then. In 2011, we completed the construction of our greenhouse in Santa Maria, California, which spans 168 acres and is the largest single-site vegetable greenhouse in the United States.”
Steven goes on: “This past year we reached another major milestone with the expansion of our facility in Delta, BC. With the addition of new greenhouses and LED lighting technology in 48 of the 92 acres at Delta, it’s now one of the largest LED-lit facilities in North America.
“We also partner with greenhouse growers in BC and Mexico who share our values and standards. Today, we’re proud to grow and market more than 2500 acres of greenhouse vegetable production supplying fresh, sustainable produce to retailers and foodservice operations across North America and Asia.”
Steven goes on to give a more specific outline of Windset Farm’s product offering: “We grow and market a diverse range of products, including tomatoes, peppers, cucumbers, lettuce, and eggplant. Over the years, we’ve expanded our range to include unique varieties with different flavor profiles, colors, and sizes, which reflect the evolving preferences of consumers. Having facilities across North America that utilize the latest technological advancements, we can offer produce to our customers all year round. This also enables us to reduce food miles, reduce food waste, and increase the region’s food security with products that are healthy and nutritious.”
Responsible farming
The business is constantly innovating its product range to keep pace with consumers’ evolving demands. One recent example Steven highlights is Sweeties™, a seedless mini pepper that’s intended to meet the growing demand for snacking varieties. “Bringing a new variety like Sweeties to market is a collaborative process. It involves market research, sourcing seeds tailored to our growing conditions and regions; running trials to test for flavor, yield, virus resistance, and shelf life, and then packing and branding. At any given moment, we’re conducting numerous trials across our greenhouse facilities to continually innovate and meet market demands.
“Alongside innovation,” Steven explains, “sustainability is also a top priority. When we built our Santa Maria facility for example, we installed one mega watt of solar panels on the roof of the packhouse, which can supply up to 20 percent of the facility’s power. For the greenhouse itself, we partnered with KUBO to construct the world’s largest Ultra-Clima greenhouse. This design utilizes both indoor and outdoor air to create an optimal growing environment. The roof is screened to prevent pests from entering and energy-efficient fans help reduce energy consumption and CO₂ emissions.
“Similarly, with our recent Delta build, we incorporated advanced technologies to ensure operations are as sustainable and efficient as possible. We collaborated with BC Hydro to utilize renewable hydroelectric power for our lit production. We also opted for LED lighting because of its energy efficiency, long lifespan, and customizable light spectrum. LEDs also produce less heat, which helps maintain ideal greenhouse temperatures. By integrating these technologies into our facilities, we’re not only improving efficiency and sustainability but also setting a benchmark for responsible greenhouse farming.”
Sustainable solutions
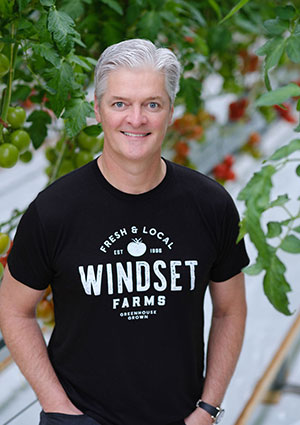
Windset Farms’ commitment to sustainability permeates all aspects of the company’s operations. Steven highlights some other key ways processes have been optimized to minimize the footprint of the business. “In our greenhouses, we use a water recirculation system that allows us to reuse 98 percent of our water. We’ve also installed state-of-the-art thermal screens that prevent heat loss, resulting in energy savings of 40 percent. Additionally, our ventilation fans and humidity sensors work together to monitor and control the greenhouse climate.
“At our Delta facility, we utilize renewable biomass boilers to heat our greenhouses. These boilers are fueled by wood waste, such as trim ends from mills, damaged pallets – including our own – and post-construction waste. The wood is burned to heat a water transport system that circulates between the greenhouses. Biomass fuel is carbon neutral because it doesn’t emit new carbon into the atmosphere, and by diverting this material from landfills we extract useful energy reducing fossil fuels like natural gas.
“On the packaging side, we’re committed to reducing plastic and incorporating post-consumer recycled content. All our punnets and clamshells contain at least 70 percent recycled material. We’ve also transitioned to mono-material PET lidding film, which reduces plastic use by 50 percent compared to previous materials. These mono-material LDPE bags reduce plastic by 20 percent compared to the alternatives.”
With recent expansions and investments, Steven is excited to see what 2025 will offer. “We’re excited to head into our first winter growing season with the expanded facility in Delta, BC. This past year, we teamed up with Buy BC brand ambassador Chef Ned Bell to create an engaging recipe series and a farm tour for our social media platforms. These initiatives are designed to educate consumers about greenhouse produce, our sustainable growing practices, and the importance of healthy eating. In the new year we’re looking forward to continuing campaigns like these for our entire market as we celebrate and support local agriculture and businesses.”
In the coming years both the BC and California plants will see further expansion as the company capitalizes on increasing year-round demand for high quality fresh produce.