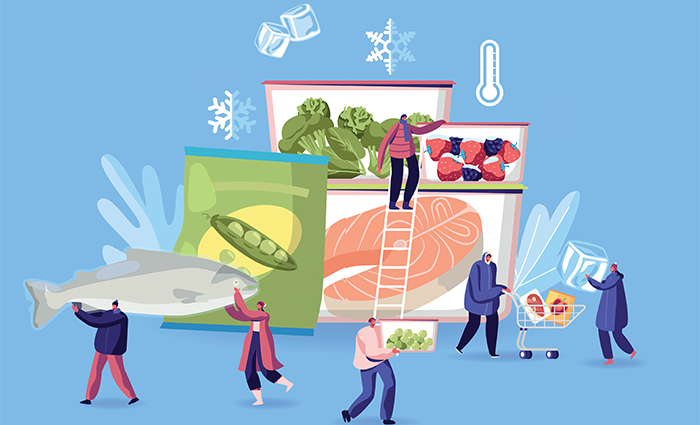
Increase confidence in supply chain predictability through smart manufacturing By Jim Bresler
Food and Beverage (F&B) manufacturers are under increasing scrutiny and pressure. Problems with empty grocery store shelves have mostly subsided since the pandemic, but F&B manufacturers still have plenty of challenges to contend with today. Key challenges include environmental volatility that can impact production, ingredient availability and transportation as well as labor shortages that impact productivity across an enterprise’s supply chain operations. Frozen F&B suppliers face an added hurdle in the industry – guaranteeing that their goods stay frozen during transportation. Logistical efficiency is essential for making sure products reach customers unscathed and at peak quality, thus cementing a successful supply chain process.
Labor shortages and environmental disruptions are expected to continue or worsen in the coming years. In response, F&B manufacturers must leverage smart manufacturing technologies to enable supply chain and production predictability. Accurate demand and inventory forecasts produce insights that enable F&B companies to develop strategies that minimize food waste and adhere to regulatory requirements. In addition, better predictability enables enterprises to circumvent disruptions caused by natural disasters and labor shortages.
Advanced inventory & logistics management challenges
The F&B industry is facing increasing demand for longer product shelf life. At the same time, regulatory agencies are examining food manufacturers through a critical lens following the events of the pandemic and the recent national baby formula shortage across the US. Further complicating operations are challenges surrounding ingredient sourcing, production planning and logistics management.
In contrast to other manufacturers, F&B manufacturers – especially frozen F&B producers – cannot depend on an easily predictable level of supply or demand. Trends in consumption and ingredient availability change over time and are subject to seasonal fluctuations in the F&B industry. Variability in ingredient quality and shipping times can also impact production planning. While frozen F&B manufacturers produce a shelf-stable item, so long as the finished product remains frozen, the ingredients used in production are still subject to degradation and potential damage.
To overcome these challenges and meet fluctuating demand, frozen F&B manufacturers must be able to scale production up or down as indicated by data-driven insights. Agile scaling of production enables F&B companies to meet demand when it rapidly fluctuates while reducing the risk of revenue lost through food waste and expired products.
Successfully executing advanced inventory and logistics management requires elevating operations beyond paper documents, which are still used for inventory and production planning by many manufacturers. Paper-based approaches to inventory sourcing and production management leads to significant obstacles in the volatile supply chain reality of today: slow internal communication, uncoordinated efforts and misaligned priorities between departments (sales, order processing, customer care and plant floor operations) and a lack of visibility into real-time updates. To get through communication bottlenecks, overcome labor shortages, effectively manage third-party suppliers and enable visibility across supply chains, which leads to predictability and traceability, manufacturers must digitize their operations.
Digitizing inventory & logistics management
Smart manufacturing technology adoption, and the digitization of processes that accompanies a smart manufacturing approach, elevate procurement and production planning and lead to maximizing revenue generation and reducing waste. It’s simply impossible to overcome the F&B supply chain challenges of today through paper processes, which cannot provide automated tracking capabilities or integrate with critical manufacturing systems such as Enterprise Resource Planning (ERP) or Manufacturing Execution Systems (MESs).
F&B manufacturers that digitize operations can leverage the Industrial Internet of Things (IIoT) and industrial automation systems to collect and analyze supply chain information. Analyzing this information generates data-driven insights to guide strategic decision-making as well as internal and external communications with stakeholders and partners. However, if insights are to be accurate, this data must be holistic – i.e., collected from across the enterprise’s various departments and systems – which is impossible to confidently achieve with a paper-based approach.
F&B companies must compare historic customer purchasing information against relevant inventory procurement data to optimize supply chain planning. But enterprises that leverage insights derived from incomplete data run the risk of basing key business decisions on faulty information. This risk is best avoided by deploying supply chain planning software, which aggregates end-to-end enterprise data into a single source of truth for analysis. Advanced analytics capabilities offered by supply chain planning software automate the generation of actionable insights based on historical data and help F&B manufacturers easily identify optimal strategies to circumvent logistics challenges. Further, the automation of data analysis and insight generation reduces the strain on human workers and frees up time to solve other challenges throughout the enterprise that cannot be solved by advanced data analytics.
Predictability is the core benefit of a smart manufacturing approach to supply chain planning. Increasing predictability of outcomes by analyzing historic procurement, shipping, purchasing and production data, enables decision-makers to visualize supply chain timelines and ingredient availability more accurately than would ever be possible with a paper-based approach.
Inventory & logistics management optimization benefits all stakeholders
Supply chains are essentially a giant collaborative project. Multiple stakeholders work together to construct and manage a supply chain from beginning to end. Partners, suppliers, distributors, freight companies and raw ingredient suppliers can all gain increased predictability, reduced waste and optimal revenue-generating strategies based on insights provided by the digitization of supply chain planning. Suppliers can receive accurate orders farther in advance, logistics providers can better plan shipping operations due to more accurate estimates of reserved freight capacity, and manufacturers can feel more confident in their partners’ ability to meet demands. These benefits will be key to ensuring business continuity when frozen F&B manufacturers must overcome the next challenge – whatever that may be.
For a list of the sources used in this article, please contact the editor.
Jim Bresler
www.plex.com
Jim Bresler is Director of Product Management, Food & Beverage, Plex. Plex Systems, Inc., a Rockwell Automation Company, is a leader in cloud-delivered smart manufacturing solutions, empowering the world’s manufacturers to make awesome products. Its platform gives manufacturers the ability to connect, automate, track, and analyze every aspect of their business to drive transformation.