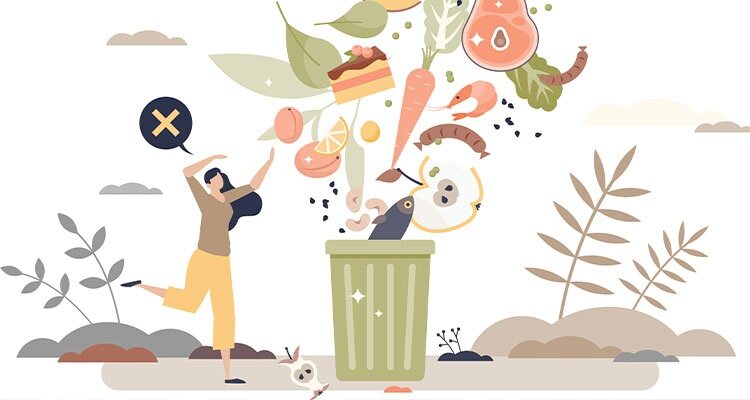
Jon Trembley, Lead Cryogenic Applications at Air Products discusses waste as a supply chain challenge
A staggering 6.4 million tons of purchased food is wasted each year from homes in the UK. The greenhouse gas emissions associated with this waste accounted for approximately 18 million tons of carbon dioxide emitted. Not only is this harmful to the environment and global climate, but it has an impact on people’s pockets too. Wasted food accounts for around £17 billion each year, equating to £250 per person.
The scale of the waste problem is no secret in the food sector and there have been significant efforts to address it, with processes such as Modified Atmosphere Packaging (MAP) being widely recognized, accepted and explored. MAP works to increase the shelf life of food products, meaning consumers have more time before spoiling, resulting in reduced waste.
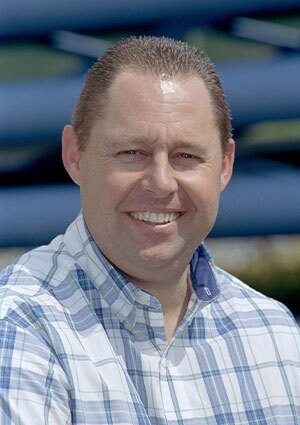
This activity has not only been with consumers and manufacturers, but throughout the whole supply chain. While the processing of food has an impact on waste, so too does its packaging. Investing in good packaging must go hand in hand with the food processing system, and there are multiple challenges to consider – not least the issue of single-use plastic packaging.
Pressure to reduce the use of these plastics which are, without doubt, a major contributor to our climate crisis, continues to grow. Meanwhile, government consultations on how food manufacturers best use different types of plastic are still ongoing.
Moving into 2024, food manufacturers will be keen to continue to ensure that products are processed and manufactured sustainably. As such, we are seeing a move from manufacturers to explore the role that freezing can play in further extending shelf life and so, further bolstering waste reduction efforts.
After all, there is no denying that consumers increasingly looking to save money and reduce waste, now seek products that have an extended food shelf-life. As a result, frozen food is growing in popularity, with independent research (commissioned by the British Frozen Food Federation in 2023), revealing that two in five consumers are now buying more frozen food than they did just a year ago. The sector has seen the frozen food market grow exponentially.
Cryogenic freezing is increasingly recognized as a cost-effective alternative to traditional methods of food freezing because of the way it supports waste reduction (during production and on the consumer side) and offers faster food production times. The fast cooling associated with cryogenic freezing enables producers to process more of their product at a faster pace, resulting in high quality products and less risk on losses due to non-optimal freezing.
Cryogenic freezers can also be adjusted across a wide range of temperatures at short notice to adapt to changing production demands easily. This allows manufacturers to move from one type of food product to another, simply and quickly. Both the equipment and the nitrogen can be configured in a way that matches the scale of the food processing operation – reducing any waste that may occur during the manufacturing process.
Rapid cryogenic chilling uses the same process method as with cryogenic freezing and manufacturers can accurately control the process according to the customer’s product requirements, and ensure constant, reliable processing and greater efficiency.
But why is speed that important? The faster a product is cooled, the faster it becomes microbiologically stable, and generally speaking, the lower the temperature, the slower bacteria will grow. Fast chilling in this way allows the food products to reach that safe holding temperature quickly. Similarly to MAP, cryogenic freezing and chilling helps to ensure the product is high quality, safe produce that has a longer shelf life, consequently reducing waste.
Ultimately, whether it’s via better packaging solutions, or improved processing through MAP or cryogenic cooling/freezing, reducing food waste is good business, economically and environmentally. Greater innovation and collaboration are key to overcoming challenges while meeting consumer demand. It’s vital that the food industry and its suppliers work together.
For a list of the sources used in this article, please contact the editor.
Jon Trembley
Jon Trembley is Lead Cryogenic Applications at Air Products. Air Products touches the lives of consumers around the globe in positive ways every day. Focused on serving energy, environment and emerging markets, the company provides essential industrial gases, related equipment and applications expertise to customers in dozens of industries, including refining, chemical, metals, electronics, manufacturing, and food and beverage.