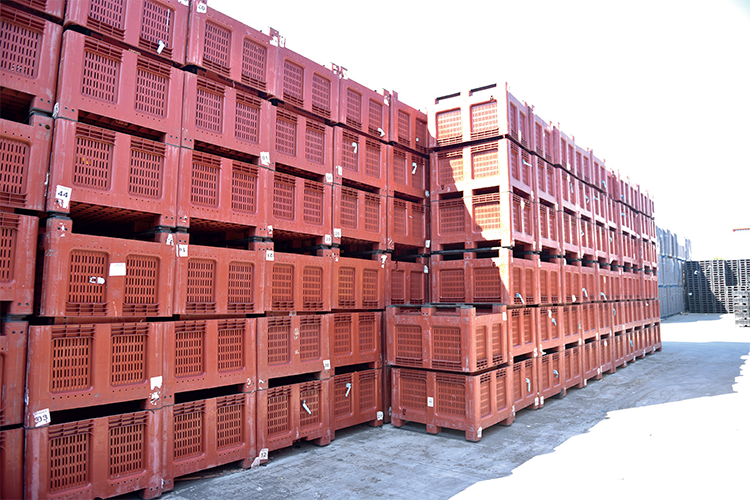
Logtek Limited
Getting down to greener business
Having been around since the late 90s, Logtek Ltd is well acquainted with the intricate work needed to put sustainability at the forefront of the packaging industry, and with its dedicated team, the business is ready for 2022 to be just as successful as 2021
In March of 2021, Logtek celebrated its 25th anniversary; a milestone that recognized its success as a returnable transit packaging solution for major retail stores such as Marks & Spencer and Aldi. “We are part of the global Schoeller Allibert manufacturing business, and started off as part of the Linpac Packaging Group,” begins Lisa Tank, the Managing Director of the Birmingham business. Born in response to customer needs and originally used mostly for produce delivery in retail supply chains, the Logtek service was a way of managing returnable transit equipment to protect and control those packaging assets. “Because there are usually several millions of pounds worth of value on our customer’s balance sheet, Logtek was created in direct response to helping grocers manage these assets around the supply chain.
“The focus is on reusing (hence ‘returnable packaging’) and it’s about moving this equipment efficiently throughout a retailer supply chain. All produce has to be transported through retail supply chains in what is referred to as secondary packaging and our job is to make sure that packaging (crates, dollies, pallets and so on) is well managed and moves through the supply chain efficiently, and are washed and repaired ready for the next cycle,” she says. Delivering this service to retail customers means that the company has been able to develop four operational sites across the UK; purely to facilitate and support this impressive efficiency.
Service delivery
Additionally, the growth in its facilities has also meant an expansion in the catalogue of products that Logtek can offer to its clients. “We built a small business in Spalding, Lincolnshire, that was originally focused on renting equipment to farmers and local agricultural businesses for seasonal use. The idea was to have rental equipment available for seasonal produce like strawberries or asparagus. That rental part of the business has consistently grown, and has allowed us to add a greater range of products. It’s not all about hand-held Maxinest trays anymore; there are dollies, pallets, and bulk containers that are used widely across the agricultural markets and meat producers.
“Now, we are widening our horizons even further with products that have been developed specifically for beverage and automotive markets for example. The Schoeller Allibert Group are supportive of growing the rental business and the focus is very much on offering all our customers, globally, a wide range of ways in which to realize savings and deliver efficiencies in using Returnable Transit Equipment. The rental service has grown significantly, and we hope that it will continue to do so,” Lisa shares.
As she emphasizes, the point of a returnable transit packaging item is to allow its use to be extended to any point in the supply chain, in order to support with sustainable and cost effective solutions and removing the use of wasteful one-trip packaging methods. “The other new piece of technology that we are building into our bulk containers is SmartLink, which is a bespoke track-and-trace system, and enables users of our rental products to see where their equipment is and moving throughout their supply chains in real time. The overall focus is on delivering value in driving efficiency and managing loss and attrition throughout the supply chain. So, it can be extremely valuable to our customers to be able to see exactly where their product is at all times and to understand cycle and dwell times especially if there is use of 3rd party logistics involved,” she informs us.
When discussing a few of the key secrets that keep the company culture united to provide an effective service and valued product, Lisa shares that the leading factor is staying true to the core values of ‘Trust, Own and Deliver’. “My view is that it is our integrity that sets us apart, and I am sure everyone else here would say the same. Although it’s a term that might sound a bit overused, for me it is about doing exactly what you say you are going to do and ensuring our customers come first. I believe that is the reason we have held our two major retailer contracts for so long. I have always believed in the perspective that looks at how we operate with people as individuals, and not only with businesses as a ‘b2b’ transaction, which means working closely with those involved. This is why I feel that our key customers renew contracts with us so consistently, because we deliver value, understand their supply chains and requirements and we work well with their people. We are a good fit. It is all about delivering a service and that is what we do first and foremost.”
Sustainable solutions
This, she continues, is why the company places enormous value on the team at Logtek, without whom the company wouldn’t be able to deliver. “We have just over 100 full-time employees across five sites; Equipment Control, admin, finance and our operations team who are on the front line doing a fantastic job and without them, we wouldn’t have a business. We do value our people, and don’t have a huge staff turnover, which I’d like to think is somewhat reflective of our culture.
“I feel that this contributes to how we are able to handle a challenge as large and overwhelming as Covid-19. By definition, the culture has always been open and supportive. It is about listening to each other, working together, and appreciating the role that everyone plays in the company. Without our people, we have nothing. Of course, the past months have been difficult and testing at times, but we managed to keep all of our operational sites open and working really well. Everyone normally office based has worked extremely positively from home. Our head office in Birmingham has only recently reopened, and we are doing three days a week at the moment on a flexible basis to ensure that the safety and wellbeing of our employees remains at the top of our list,” she shares with us.
As we come down from the peak of the pandemic, Logtek is going to continue to realign its priorities to put sustainability at the forefront of its operations. “I think compared to 2020, this year has shown how capable we are of contributing to a greener supply chain. We are expecting ten percent growth on last year, which is quite an encouragement. This has allowed us to look towards goals for 2022, and in planning our five-year timeline, which will see us looking at even more new rental products and associated services. In light of this vision, we are not leaving behind our core business, which is all about returnable transit asset management and working with our key retailers, which is always going to be the corner stone of what we do,” Lisa says.
Now more than ever, it is crucial to be embracing the principle of reduce, reuse and recycle. “It makes more sense for our customers and for people to consider using returnable packaging solutions. Our Schoeller Allibert mantra is all about ‘Making Plastic Packaging too Good to Waste’ with the emphasis on reuse and then recycling. At Logtek, we are going to be innovating that message to our full capacity for as long as we can,” concludes Lisa. It is encouraging to see businesses like Logtek, which are absolutely passionate about acting on sustainability and environmental messages to contribute to a greener future.
www.logtek.com